Home > Insulation Air Scrubber Water
Insulation Air Scrubber Water
Filtering out tiny fiberglass particles from process water is a critical part of the fiberglass insulation manufacturing industry. Producing fiberglass insulation requires the use of a lot of water for various applications throughout the plant. One critical area is the Air Scrubber Water.
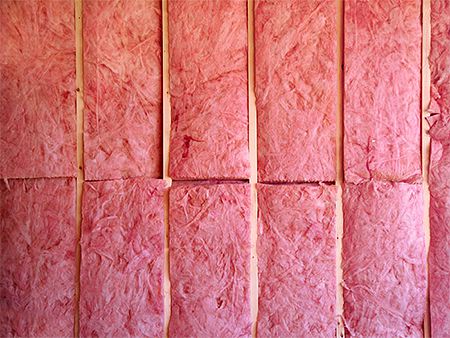
In the fiberglass insulation manufacturing process, rapidly moving air moves the small glass particles / fibers. These glass fibers are sprayed with a quenching water initially after production to cool them and solidify the glass. Glass fibers destined for batt insulation are also sprayed with a mixture of water and a sticky binding agent at this time. Air continues to move these glass fibers to various areas of the plant for making loose fill, batt insulation, etc. Most of the glass fibers go where they are needed, but this transport air still contains a high concentration of tiny glass particles.
To extract the glass particles from this air, the air passes through “scrubber” units, where water is sprayed through the air to help attract and bind up the glass particles. After the air is scrubbed, and the majority of the glass particles are removed, this air then passes through various types of air filtration and/or cleaning units for a final cleaning. Some companies use very large and expensive Electrostatic Precipitators (EPs) for this final cleaning, because after this, the air enters the plant’s exhaust / vent stack, where it typically needs to meet very stringent environmental standards and requirements for being released into the environment. The EPs or other types of air filtration and cleaning equipment is typically the last line of defense to make sure the plant’s exhaust air is clean and it meets standards. The cleaner the air is when it arrives for the final cleaning process, the more effective the process will perform, and the less the plant will have to be shut down for expensive cleaning. Thus, to get the air as clean as possible, it is absolutely critical for the air scrubbers to perform the best they can. For this to happen, the water being used in the scrubbers, which is continually recycled / reused, needs to remain as clean as possible at all times. This is where the CentraSep® centrifuge system comes into play.
The air scrubber water is typically in a closed loop, continually being captured, cleaned and reused. Various types of filtration units are used to clean this air scrubber water, including shaker screen filters, filter presses, etc., but the CentraSep system is more efficient and effective than anything else. The CentraSep system filters out the smallest / finest of particles, eliminates the expenses of disposables, reduces labor and maintenance dramatically, and more, and all while “continually” processing the air scrubber water.
The centrifuge can process this water at varying rates depending on the need. As an example, in a 50,000 gallon system running continuously (24/7), the CentraSep system can drop the solids in the scrubber water from a typical number like 24,000 ppm (parts per million) to an incredibly low 200 – 300 ppm, which is well below most companies’ needs, but that is the beauty and efficiency of the CentraSep system. Most importantly, the system “maintains” it at that level continuously. Also, the separated material coming out of the centrifuge is quite dry, like a damp stack of newspaper. This relatively dry solid material is easy to dispose of and requires no further processing.
The CentraSep system is capable of this significant level of solids reduction, due to its unique, proprietary and patented design. The CentraSep unit is vastly different from all other industrial centrifuges. It is the only single-motor, vertical, self-discharging, automatic centrifuge on the market. It combines an innovative bowl/blade clutch design with a single AC motor and variable frequency drive (see cutaway illustration) to automatically extract particulate from virtually any liquid at a wide range of processing flow rates. CentraSep centrifuges are able to remove up to four times the quantity of solids / fines that traditional centrifuges can. Also, every component of the CentraSep system that comes into contact with the process fluid is 316 stainless steel, so harsh acidic and caustic fluids, as well as hard and extremely abrasive materials like fiberglass fines, can be processed safely and effectively.
Maintaining a clean, low ppm level of solids in the scrubber water allows the air scrubbers to “continually” perform at their best, which means the air feeding into the electrostatic precipitators or other final air cleaning equipment is now much cleaner and that equipment doesn’t have to work as hard or be shut down and cleaned as often. It also means that a lot more of the glass particles are being scrubbed out of the transport air. In insulation manufacturing plants that do not have CentraSep equipment, they often experience an ineffective and inconsistent filtering process, which also leads to production inefficiencies and shutdowns, as well as very expensive and time consuming cleaning processes. Dirty water sump pits can build up glass particles until they have to be manually cleaned, which is a costly process that entails stopping production and replacing very large amounts of water (possibly 30,000 – 50,000+ gallons). Also, with more fine glass particles in the dirty sump water, the shaker screen filters and/or filter presses are continually clogging, as are the air scrubber spray nozzles. These issues require a lot of costly manual cleaning, which means more production issues, inefficiencies and shutdowns.
But regardless of how bad these issues may be prior to installing a CentraSep system, the most critical and costly problem is that the air scrubbers cannot perform at their best, and the dirty air filled with fine glass particles puts a huge strain on the electrostatic precipitators or other final air cleaning equipment the company is using. These systems continue to perform as they need to, cleaning the exhaust air to meet all the environmental regulations, but since they have to capture so much glass fiber material, they need to be shut down and cleaned often. In addition to the costly production downtime, the cost of cleaning this equipment, which often needs to be done by an outside firm, is very expensive. With a CentraSep system in place, these air cleaning systems don’t need to be cleaned near as frequently, which creates a substantial, very tangible and direct cost savings (perhaps in the tens of thousands of dollars per month).
Thus, the payback / ROI on a new CentraSep system is often less than one year, and then those cost savings continue in all subsequent years, adding up to a very substantial sum of money saved by the company. And of course this cost savings is in addition to the increased productivity, loss of downtime and the overall increased efficiency of the plant’s entire production process.
The Filtration Engineers at Trucent use their knowledge of glass, metal and other fine particle separation, to work with insulation manufacturers and solve their water filtration problems. Calculations are made and tests are performed, then the installed centrifuge unit is monitored closely to fine tune the flow rate, the dump cycle time, and the overall system performance. Trucent's Jeff Beattey stated, “Many of the insulation companies we work with have been dealing with this major filtration problem for many years, and they have tried multiple methods and nothing works. So they are often skeptical that our system will work like it does, but we have hundreds of centrifuge systems all around the world, in a multitude of harsh environments, separating all types of very fine materials, and many of those systems have been running for over 2 decades, so we have a great understanding of how our systems perform and what they can do. We are confident that we can dramatically improve an insulation plant’s water filtration processes.”
Benefits of the CentraSep Insulation Process Water Filtration System:
- No Disposables
- Fully Automatic System
- Lowest Maintenance in the Industry
- Reduced Labor
- Extended Process Water Life
- Reduced Pollution and Environmental Impact
- Standard 316 Stainless Steel Construction
- Solid Separation to the Single Micron Capabilities
- LIFETIME WARRANTY option available
CentraSep is more than a centrifuge. It represents the experience, innovation, and commitment of a comprehensive Filtration Engineering Solutions Company.
Talk to one of our Trucent Engineers today to see how we can help with your fiberglass insulation process water filtration and separation needs.
Top of Page